The can beer filling line is an optimal solution for manufacturers of alcoholic beverages, beer, and soft drinks, featuring modern and precise filling and can sealing technology. This system not only improves productivity but also ensures product quality, meeting the stringent standards of the food and beverage industry.
The can beer filling line is equipped with advanced filling technologies, synchronizing all stages, from filling and can sealing to the final product packaging. The seamless operation of these processes helps minimize product centrifugation, protecting the product from oxidation throughout the production process.
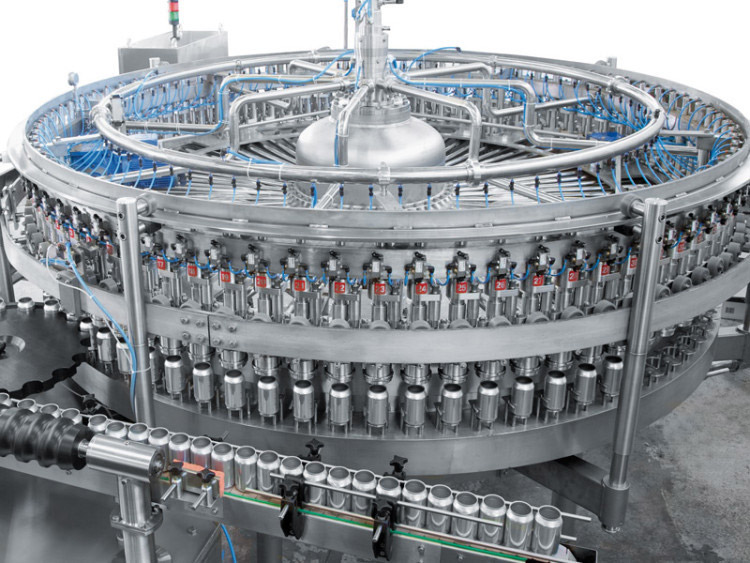
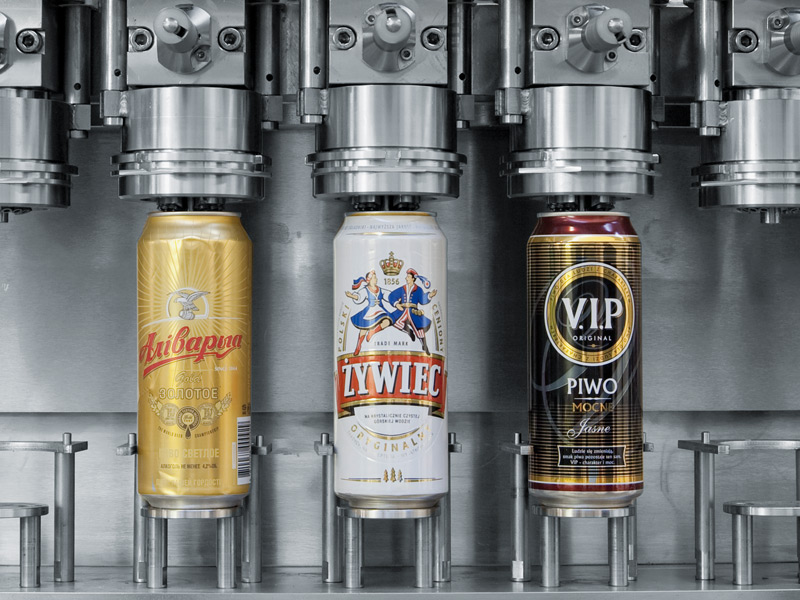
Detailed Operating Process of the Can Filling Line
- Filling and Sealing
The can filling line uses advanced technology to protect the product from oxidation and ensure quality in every can. The steps in the filling and sealing process include:- The beer tank is completely isolated from the air and is combined with an inert gas pump to prevent oxidation of the beer during the filling process.
- A dual inert gas pump is used inside the can before filling, creating a clean air environment that helps preserve the product’s original flavor.
- The gas is vented through separate pipes to minimize contact with oxygen.
- An inert gas pump before sealing ensures product stability and facilitates quick and accurate can sealing.
- The caps are guided through a cap feeder with a “no can, no cap” sensor, enabling full automation and preventing cap loss if there is no can.
- The automatic can sealing process helps save time and effort while maintaining a perfect seal for each can.
- Palletizing Preparation
The palletizing process is automated and includes the following steps:- The cans are stacked into layers accurately and evenly.
- The system automatically stacks and separates layers to ensure that goods do not mix.
- A high-speed vacuum lifter assists in moving and arranging cans onto the pallet quickly and efficiently.
- X-ray Quality Inspection
Modern X-ray technology is used to check for any foreign objects that may be inside the cans, ensuring complete safety for the product. Defective cans or those not meeting standards are pushed out of the system, minimizing the risk of compromising the final product quality. - Heat Drying Tunnel and Steam Dryer
The heat drying tunnel is specially designed to reduce the amount of water condensation on the cans. Afterward, the steam dryer ensures the cans are completely dry before they are printed with production dates, ensuring there is no excess moisture during printing and packaging. - Date Printing
The can filling line uses continuous inkjet printing technology to print expiration dates, barcodes, logos, and other information on the cans. This technology allows for quick and accurate printing, meeting the product preservation and management requirements. - Packaging
The packaging section of the can filling line may include the following optional steps:- Palletizing: Cans are packaged into smaller bundles, making it convenient for transportation and consumption.
- Carton Packing: Cans are packed into cartons for easy transport.
- Stretch Film Pallet Wrapping: Ensures product safety and security during transportation and storage.
Advantages of the Can Filling Line
- Advanced technology helps optimize the production process, increase productivity, and minimize waste.
- Protects the product from oxidation, preserving the flavor and quality.
- The quality control system ensures consumer safety.
- High automation reduces human intervention, saving labor costs and increasing work efficiency.
- High flexibility allows the line to meet the production needs of various types of products.
With this modern can filling line, manufacturers can not only improve production efficiency but also protect product quality, thereby meeting the growing market demands.